Drape Forming
Home » Plastic Forming & Fabrication Services » Thermoforming » Drape Forming
Drape Forming is one of the many manufacturing processes that we use among the varied techniques that we have. Drape forming is the ideal method for creating plastic components in which a gentle curving or other shaping is needed, as sometimes a design will require a highly specific and precise curvature for its application.
We design and build a bespoke forming mould for each unique product being produced. The manufacturing process is specialised but in its simplest form it is heating up a plastic sheet to the desired temperature, making the material flexible, and then draping it over the mould. It settles into the desired shape and then is covered with a layer of soft moulding cloth until it forms rigidity as it cools.
At ASH Plastics Ltd we can offer drape forming using several types of plastics and up to 1200mm x 2500mm in measurement. We can also do large scale product orders making sure that the last item produced is identical to the first.
At A.S.H. Plastics we utilise many manufacturing techniques. Together with drape forming we also do; laser cutting, line bending, dome blowing, polishing and bonding.
Whatever your requirements are, we can offer you a solution that is affordable and obtainable.
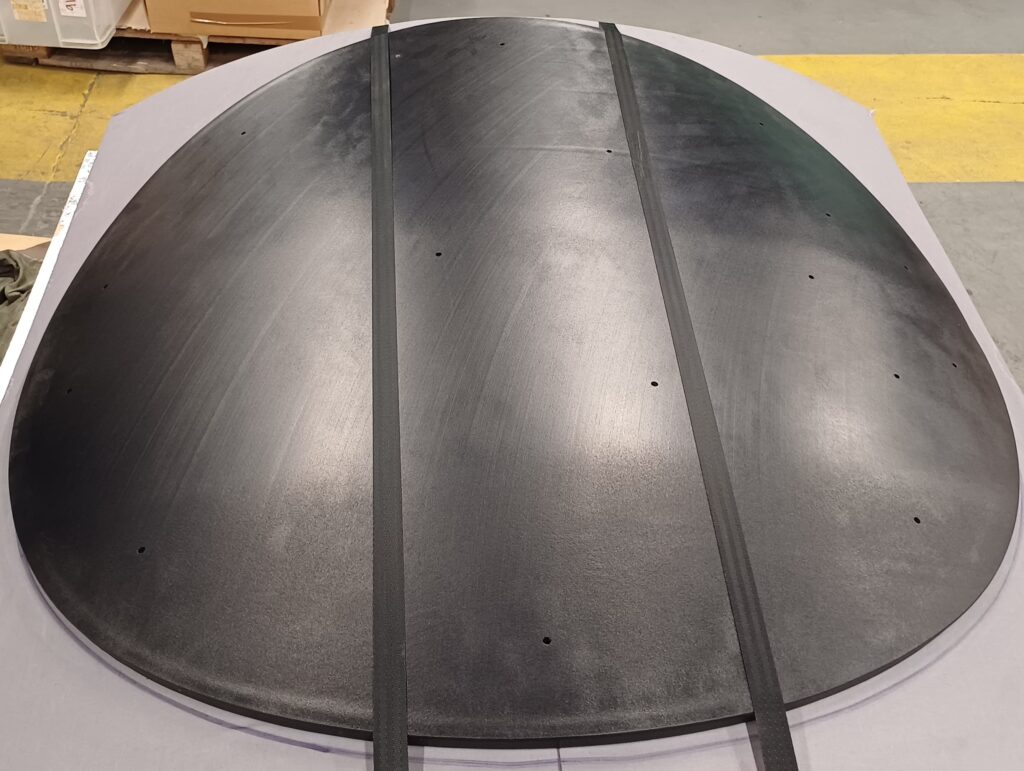
Get in touch
We work with some of the biggest retail brands in the UK and many smaller independent retailers and businesses and we are ready to take on the next big industry challenge, that might just be your challenge too! Why not get in touch with us today.